skirt support design calculation
C E WELD JOINT EFFCIENCY 085 CA CORROSION. Lets use me as an example again.
17 How To Add A Skirt To A Pressure Vessel Autopipe Wiki Autopipe Bentley Communities
Operating weight of the vessel.
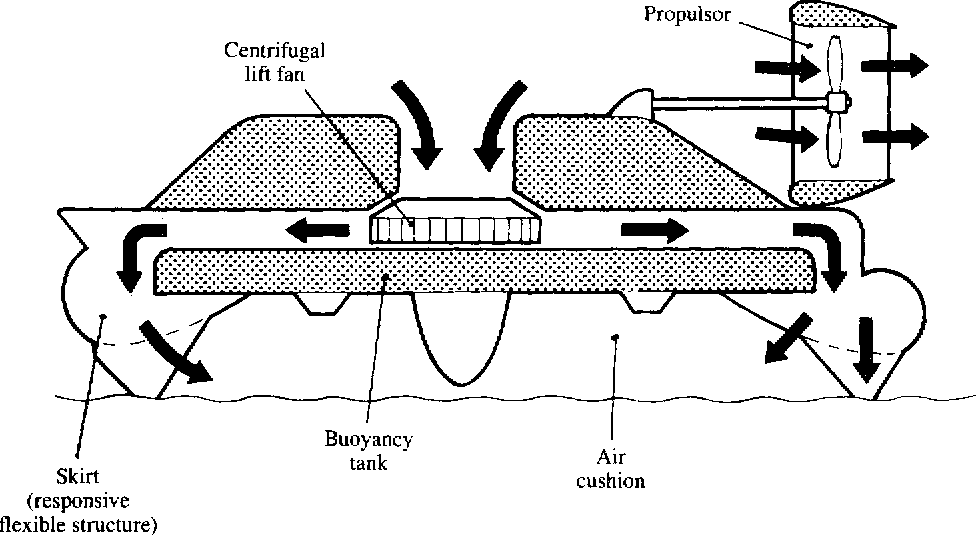
. Dead weight of the vessel. Average Skirt Temperature Calculation Output Values. Vseismic css CvI W 29 0331 1073680 There are Maximum and Minimum limits for Design base shear which have been proposed in UBC-1997.
Skirt is a cylindrical section that forms the interface to the cylinder or connection flange the wall thickness of which should be at least the same as the vessel to which it is attached. Design Calculations Deisohexanizer Reboiler E-610 29 July 2010 Revision. Hence we require skirt support.
SAMPLE DESIGN CALCULATION - SKIRT SUPPORT DESIGN OF VERTICAL COLUMN REFERENCE Pressure Vessel Design Manual by Dennis R. Lot of considerations required superimposed loads internals liquid attachments loadspipingseismicwind lifting temp. The various vessel-supporting methods are discussed.
Lateral loads by restrained thermal growth of interconnecting pipes. Skirt support is designed by considering the following loads. Various types of skirts are available such as cylindrical conical lug support on vessel conical support on shell leg support etc.
Assume a thickness of 10 mm for the support skirt and the mean diameter of the support as 425 m. The bolt circle diameter of the support may be assumed to be 45 m. The support skirt is a component that operates at elevated temperatures and.
The design of process columns and supporting skirts is a complex subject and should only be undertaken by someone with a graduate level engineering degree in structures. Moss VESSEL DESIGN DATA AND WEIGHT CALCULATION CODE ASME SEC. 3 x wall thickness half an inch.
Columns of diameters greater than 600 mm are usually mounted on the skirt support. If your current pressure vessel software does not include support skirt openings its time to explore the many benefits of COMPRESS. T ri vz-l ro vz-1vz where z sep se-p the equation for ellipsoidal head thickness is given by t pdi 2se02p pdo 2se18p where t minimum required thickness of the ellipsoidal head exclusive of corrosion allowance p design pressure or maximum.
If you bend to the side the crease that forms is your natural waistline Dont suck in your stomach or youll measure inaccurately. Correction Factor Δ T F Δ T 1. 104962 Microprotol 32905 - Jul 2010 procal V32905 - 01072010 8 prodia2 V32905 - 1072010 EuResearch Input data list Design Parameters.
Skirt Design The cylindrical shell of the skirt is designed for the combination of the stresses due to vessel dead weight wind load and seismic load. See VIII-1 UG-23 b. This paper describes the considerations employed in the finite element analysis of a relatively short support skirt on a hydrocarbon reactor vessel.
Which skirt is applicable and need to attach for. Design of supports. Heres the basic formula for a half circle skirt.
Ceilings it is supported by a skirt which is welded to the bottom head. The analysis is accomplished in accordance with ASME BPV Code Section VIII Division 2 alternate rules in conjunction with the guidelines outlined in WRC Bulletin 429. The half circle skirt uses our waist circumference in a semi-circle rather than the full circle we used in the formula above.
Material of your skirt anchoring etc. To measure the circumference accurately wrap the tape measure around your waist like a belt at your natural waistline located above the belly button and below the rib cage. Wind load acting over the vessel.
Design a skirt support for a pressure vessel with a total vertical load of 720 kN and an overturning moment of 2050 kNm. Waist for a half circle skirt 2C SA 2Ï€. The ability to add pipe elbows reducers and piping that extends through the skirt opening has also been provided.
The final design should be certified and stamped by a professional engineer and checked by others. Seismic load To calculate the skirt thickness all these loads are required to be considered. Many researchers have attempted to design and analyze support structure of vessel 1 2.
F Average Skirt Temperature T1 F r0-012811 Please fill all required fields. Skirt hcss 240 Inch 6096 mm Elastic period of vibration Tcss Ct he075 0035 20075 0331 s 0768125 shell dished end etc of vessel. Find out more by clicking on the button below or calling us 941 927-2670.
General Configuration of a typical pressure Vessel This basic formula is modified in international design codes. These affects your skirt thickness its time consuming wish that somebody can help you to run thru software. Height of CS.
This means we need to double our waist measurement to find the right radius. Average Skirt Temperature T1 F r0-012811. All head volumetric calculations include a skirt length equal to the minimum value recommended by ASME of.
Insulation Coefficient psi K h t 05. Pressure Vessel Design Formula The basic formula for designing the cylindrical shell is σ PD2t Therefore t PD2σ Where t thickness of the shell P internal pressure D diameter of the shell σ tensile stress Fig. Though Section VIII does not deal with support design it is common to determine the compressive stress due to weight and bending and use Section VIII allowable longitudinal compressive stresses as the acceptance criteria.
1 LATEST P DESIGN PRESSURE 60 FV Barg T DESIGN TEMPERATURE 250 Deg. AD-MERKBLAETTER 2000 11-2007 Karman Effects Prevented by 3 Helicoidal Plates at 120.